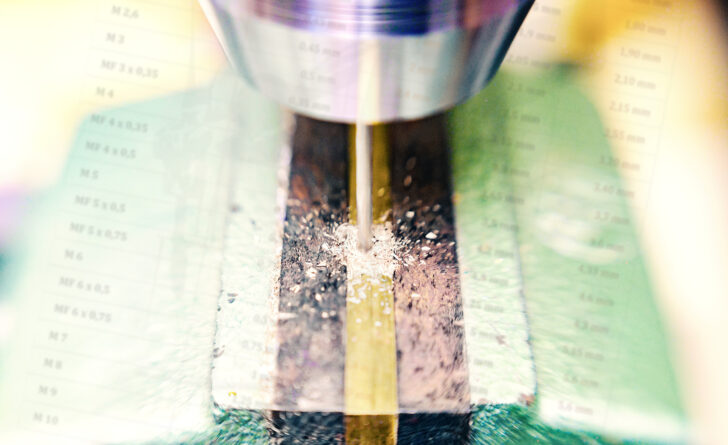
Das Schneiden metrischer Gewinde in ein bereits vorhandenes Kernloch gehört zur Standardanwendung des Modellbauers im Feinblechbau, wie auch im Metallbau insgesamt. Nicht selten sind Löcher für Gewinde in Bausätzen auch nur vorpunktiert und müssen vor dem Schneiden mit einer eigenen Kernlochbohrung selbst noch auf die benötigte Größe gebohrt werden. Eine Tischbohrmaschine wird vermutlich auch jeder im Hobbykeller haben, aber welche Kernlochgröße ist nun die Richtige für mein Gewinde?
Kernlochtabelle: Der richtige Durchmesser zum Gewinde
Norm | Steigung | min. ∅ | DIN ∅ | max. ∅ |
---|---|---|---|---|
M 1 | 0,25 mm | 0,7 mm | 0,75 mm | 0,78 mm |
M 1,2 | 0,25 mm | 0,8 mm | 0,9 mm | 0,98 mm |
M 1,4 | 0,3 mm | 1 mm | 1,1 mm | 1,14 mm |
M 1,6 | 0,35 mm | 1,2 mm | 1,25 mm | 1,30 mm |
M1,7 | 0,35 mm | 1,2 mm | 1,3 mm | 1,35 mm |
M1,8 | 0,35 mm | 0,4 mm | 0,45 mm | 1,48 mm |
M2 | 0,4 mm | 1,5 mm | 1,6 mm | 1,68 mm |
M 2,2 | 0,45 mm | 1,6 mm | 1,75 mm | 1,80 mm |
M 2,3 | 0,4 mm | 1,8 mm | 1,9 mm | 1,90 mm |
M 2,5 | 0,45 mm | 2 mm | 2,05 mm | 2,10 mm |
M 2,6 | 0,45 mm | 2 mm | 2,1 mm | 2,15 mm |
M 3 | 0,5 mm | 2,4 mm | 2,5 mm | 2,55 mm |
MF 3 x 0,35 | 0,35 mm | 3,1 mm | 3,15 mm | 3,20 mm |
M 4 | 0,7 mm | 3,2 mm | 3,3 mm | 3,40 mm |
MF 4 x 0,35 | 0,35 mm | 3,6 mm | 3,65 mm | 3,7 mm |
MF 4 x 0,5 | 0,5 mm | 3,4 mm | 3,5 mm | 3,6 mm |
M 5 | 0,8 mm | 4,1 mm | 4,2 mm | 4,33 mm |
MF 5 x 0,5 | 0,5 mm | 4,4 mm | 4,5 mm | 4,6 mm |
MF 5 x 0,75 | 0,75 mm | 4,2 mm | 4,25 mm | 4,3 mm |
M 6 | 1 mm | 4,8 mm | 5 mm | 5,15 mm |
MF 6 x 0,5 | 0,5 mm | 5,4 mm | 5,5 mm | 5,6 mm |
MF 6 x 0,75 | 0,75 mm | 5,4 mm | 5,5 mm | 5,6 mm |
M 7 | 1 mm | 5,9 mm | 6 mm | 6,15 mm |
M 8 | 1,25 mm | 6,7 mm | 6,8 mm | 6,90 mm |
M 9 | 1,25 mm | 7,7 mm | 7,8 mm | 7,90 mm |
M 10 | 1,5 mm | 8,4 mm | 8,5 mm | 8,60 mm |
Die Tabelle für Metrische Gewinde und Feingewinde zum Ausführen einer Kernlochbohrung gibt es auch als PDF zum Ausdrucken. So hängt es nun auch bei mir im Hobbykeller und ich sehe mit einem Blick, welches Kernloch ich für mein Gewinde bohren muss.
Was ist ein Kernloch überhaupt?
Ein Kernloch ist entweder ein Sackloch oder Durchgangsloch im Werkstück, welches in aller Regel aus Metall oder einer Metalllegierung ist. Gewinde in Plastik und Holz gibt es zwar auch, aber eher seltener. Nachdem das Kernloch gebohrt ist, kann im zweiten Schritt hierein ein Gewinde geschnitten werden. Das Loch ist je nach zu schneidendem Gewinde gemäß der Tabelle zu bohren oder zu fräsen, seltener auch mal zu drehen, wenn es sich ergibt. Mit der richtigen Kernlochgröße stellst Du sicher, dass eine später einzudrehende Schraube sicher im Werkstück sitzt und eine gute Verbindung bietet.
Im Grunde kann man sagen, dass das Kernloch die Größe einer einzudrehenden Schraube ohne Außengewinde, die Lamellen, hat.
Toleranz beim Bohren eines Kernlochs
Gerade im Hobbybereich hat man häufig ausgerechnet nicht die richtige Bohrergröße zur Hand und muss sich, wie so oft, behelfen. Die gute Nachricht ist aber nach meiner Erfahrung, dass man je nach Qualität des Gewindeschneiders und der Anwendung für das spätere Gewinde, man durchaus ein wenig (!) Toleranz bei der Wahl de Kernlochgröße hat. Du kannst im Zweifel also auch das eine oder andere Zehntel Millimeter kleiner, oder je nach Material auch ein etwas größeres Kernloch bohren. Beides hat allerdings Nachteile, sodass man es hier keinesfalls übertreiben sollte! Die Toleranz nach oben (größeres Kernloch) ist deutlich kleiner als die nach unten (kleineres Kernloch). Die Toleranz nach unten ist wesentlich von Material und Gewindeschneider abhängt.
- Größer bohren als das Kernloch-Maximum solltest Du bei weichen Materialen vermeiden. Hier läufst Du sonst Gefahr, dass die einzudrehende Schraube nicht mehr sicher greifen kann und schnell ausleiert.
- Kleiner bohren erhöht die Gefahr eines Gewindeschneider-Bruchs exponentiell, vor allem in harten Materialien. Ein dreifach Gewindeschneider hat in der Regel weniger Probleme mit etwas zu kleinen Kernlöchern, da man ja dreimal nacheinander Material vom Werkstück abträgt.
Meine Erfahrung: Es ist durchaus verzeihlich, wenn man für ein typisches M2 Gewinde mit einem gebräuchlichen 1,5 mm Bohrer das Kernloch setzt, statt einem geforderten 1,6 mm Bohrer. Noch kleiner werden als 1,5 mm sollte man aber auf keinen Fall und größer als 1,7 mm im M2 Beispiel führt zu viel Spiel im Gewinde, sodass sich die Schraube kaum mehr von selbst halten kann.
Formel zur Berechnung des Kernlochmaßes
Wer die Tabelle aufmerksam studiert kann feststellen, dass sich eine einfache Formel zur Berechnung des Kernlochdurchmessers anwenden lässt. Voraussetzung dafür ist allerdings, dass man die Steigung kennt. Hat man diese, zieht man sie einfach vom Durchmesser der ISO-Schraube ab. So lautet die Faustformel:
Kernlochmaß = Durchmesser – Steigung
Beispiel für M6: Durchmesser ist M>6< = 6 Millimeter Außendurchmesser. Die Steigung eines M6 Gewindes ist 1 mm. Daraus ergibt sich ein Kernlochmaß von 5 mm. Zugegeben: Eher kennt man die Kernlochgröße als die Steigung, zumal die bei metrischen ISO Gewinden auch nicht im Namen genannt wird. Oder weißt Du auf Anhieb ohne nachzuschauen, welche Steigung eine M 2.5 Schraube hat?
Welcher Bohrer für ein Kernloch?
Es benötigt erstmal keine speziellen Bohrer für eine Kernlochbohrung, der normale Metallbohrer ist hier das Mittel der Wahl. Allerdings sollte das Bohrloch natürlich exakt 90° zur Werkstückoberfläche sein, damit die dort hineingedrehte Schraube auch plan auf dem Werkstück aufliegen kann. Allzu günstige Baumarkt-Tischbohrmaschinen neigen leider immer wieder dazu, dass der Bohrer ausschlägt und das Bohrloch so größer wird als benötigt. Außerdem ist die Winkeligkeit auf günstigen Tischbohrmaschinen nicht immer wirklich gegeben. Was für den Feinblechbau komplett ausscheidet, ist der Akkubohrer.
Eine Besonderheit beim Bohren stellt das beliebte Messing dar. Hier neigt der Standardbohrer durch seinen Anschliff dazu, zu verziehen. Vielleicht ist es Dir auch schon einmal passiert, dass Du ein Durchgangsloch von oben in ein Vierkant gebohrt hast und auf der anderen Seite nicht mehr zentriert herausgekommen bist? Das ist ein klassisches Problem eines Bohrers, der sich im Material verzieht. Für Messing gibt es spezielle Bohrer die genau das vermeiden! Durch eine andere Bohrerspitze wird dieses Problem umgangen sodass gerade in das Material eingetaucht und durchgebohrt werden kann.
Ganz grundsätzlich kann man immer nur so gut arbeiten, wie es das Arbeitsmaterial zulässt. Ich verwende für Messing mittlerweile ausschließlich Bohrer von Löher aus Remscheid, so viel Lokalpatriotismus sei gestattet. Da kann ein einzelner Bohrer schon einmal ein paar Euro kosten, aber das tut nur einmal weh. Schlechte Bohrergebnisse ärgern hingegen immer wieder aufs Neue.
Das Kernloch bohren
Der typische Anwendungsfall im Modellbaubereich ist natürlich die Tischbohrmaschine. Zum Bohren des Kernlochs gilt, was auch für das normale Bohren gilt:
- Werkstück anreißen und körnen
- Werkstück im 90° Winkel zur Oberfläche ausrichten, in die gebohrt werden soll
- Werkstück sicher fixieren und gegen verrutschen oder ausschlagen sichern
- Mit Drehzahl gem. Werkstoff, Bohrer und Stärke bohren
- Angepasster Vorschub und gegen Überhitzung zu schützen, ggf. kühlen
Kernlöcher mit CNC Fertigung
Im Rahmen der CNC Fertigung übernimmt mittlerweile häufig die Fräsmaschine das „Bohren“ der Löcher, sei es, dass direkt auf Maß mit einem echten Spiralbohrer gebohrt wird, oder ein entsprechender Fräser bohrt oder ausfräst. Die Funktion der Kreistasche ermöglicht exakte Kernlöcher. Kernlöcher sollten immer schonend gebohrt oder gefräst werden, damit möglichst wenig Hitze entsteht. Hitze kann schnell zu einer Verhärtung des Bohrrands führen, wodurch sich, je nach Material, das spätere Einbringen eines Gewindes erheblich erschwert. Hier droht dann auch schnell ein Gewindeschneiderbruch. Wenn Du einen entsprechenden Spiralbohrer oder Fräser einspannst, kannst Du natürlich auch manuell mit der Fräsmaschine über das Koordinatensystem wunderbar Kernlöcher bohren.
Bei einer so genannten Kreistasche verfährt der Fräskopf jeweils an der Innenkante des auszufräsenden Kernlochs entlang und fräst sich so Stück für Stück durch das Material. So kann ein beliebiger Kreisdurchmesser realisiert werden, der größer oder gleich des Durchmessers des Fräsers ist. Da hierfür pausenlos jede Achse verändert wird, ist natürlich eine exakt arbeitende Fräsmaschine ohne Umkehrspiel unbedingte Voraussetzung.Kernloch mit Reibahle auf Maß bringen?
Mit einer Reibahle kannst Du ein Loch mit wesentlich höherer Präzision auf ein gewünschtes Maß bringen und für eine bessere Oberflächengüte sorgen. Allerdings ist die Reibahle in der benötigten Kernloch-Größe vermutlich noch seltener im Hobbykeller vorhanden, als der benötigte Bohrer.
Erschwerend kommt hinzu, dass Du für eine Bohrung mit späterer Bearbeitung mit der Reibahle auch noch wenige Zehntel auf Untermaß bohren musst. Auch dafür brauchst Du dann auch noch mal einen entsprechenden Bohrer. Zusätzliche Zeit musst Du natürlich überdies noch mit einplanen.
In der Praxis ist das alles nicht wirklich praktikabel für „normale“ Löcher, sodass die Verwendung einer Reibahle für Kernlochbohrungen keine Verwendung findet. Wenn einfach nur zwei Bleche miteinander verschraubt werden, reicht ein normal gebohrtes Kernloch vollkommen aus. Wenn es jedoch um Gewinde an Ventilen geht, so nutze ich gerne einmal eine Reibahle, um für möglichst sichere und dichte Führung des Gewindes sorgen zu können.
Ein Kommentar
| »
Hallo,
tolle Tabelle und prima Erläuterungen zu den modellbaurelevanten Punkten!!!
Grüße von der wwo (Wald+WiesenbahnOßweil)
Andreas